Warehouse Safety and Risks
Posted on: 18/10/2018, 12:37
What’s in store for warehouse safety?
Warehouses, by their nature contain many opportunities for accidents – be they from heavy duty machinery and equipment to storage of potentially hazardous or heavy items. Identifying where the hazards may occur is the first step in the safety process and by following the appropriate legislation, as well as some general common sense guidelines, you can lessen the risk of serious injury in your workspace.
Identifying warehouse risks
Under the Health and Safety at Work Act 1974 employers have a responsibility to ensure, so far as is reasonably practicable, the safety of employees and visitors and to minimise the risk of accident and injury.
Some of the main risks to be aware of in a warehouse include slips and trips which, according to the HSE, are the leading cause of non-fatal workplace injuries in the UK. In warehousing, slips will be most commonly caused by wet or contaminated floor surfaces. Preventative measures to avoid slip accidents involve cleaning up any spills immediately and displaying the appropriate warning signs when the floor is known to be slippery. Trips can be caused by simple reasons such as discarded straps, ties and other waste packaging. Workers can be reminded of the importance of general good housekeeping via prominently displayed posters.
Manual handling can lead to work-related musculoskeletal disorders which accounted for 8.9 million working days lost in 2019/20, across all industry, according to the HSE. Manual handling should be avoided where possible and alternative solutions such as lift and pallet trucks should take the strain. Although, it should be noted that this type of machinery can come with its own risks, such as crush injury, so will require appropriate training and supervision. If manual handling is unavoidable then the risk of injury can be minimised by undertaking a manual handling assessment.
According to RIDDOR, falls from height are the leading cause of all fatal injuries, accounting for 29 people killed in 2019/20. The first rule of working at height is to avoid doing so however, if this is not possible, the correct safety equipment must be identified and workers trained in how to use it. Warehouse racking or shelving is not designed for being climbed on so should not be used for access. Ladders can be a viable option for working at height, particularly for jobs of short duration however, as with all equipment; they should be regularly maintained and checked for defects which are easily communicated to potential users via documented risk assessments and ladder tags. Again, users should be trained in how to use ladders according to specific manufacturer guidelines.
Racking
Being struck by a moving or falling object was the cause of 18 workplace fatalities in 2019/20. In a warehouse, preventing this type of injury is largely focused on stacking items safely. Racking systems are widely used in warehouses as they offer considerable space advantages over floor storage while providing easy access and retrieval of items. There are many different types of racking system but as a general rule, racking systems should be of solid construction and material with adequate strength for the job and installed and maintained in accordance with the manufacturer’s instructions. Racking should have clear tagging securely fixed to it, stating the maximum load together with any necessary specified load stipulations.
Racking should also be inspected on a regular basis as damage to racking is the leading cause of rack system failure. Racking tags can make this process mush easier – Centurion’ Europe’s racking tags are designed to be fixed to the crossbeams of the racking. The checklist on the insert describes the checks which must be made and inspection details can be recorded. If the racking is deemed to be unsafe, the insert can be removed and replaced with a Do Not Use Unsafe Racking message.
The frequency of inspections varies between warehouses and should be determined by a nominated ‘person responsible for racking safety’ to suit the operating conditions of the warehouse.
Vehicles
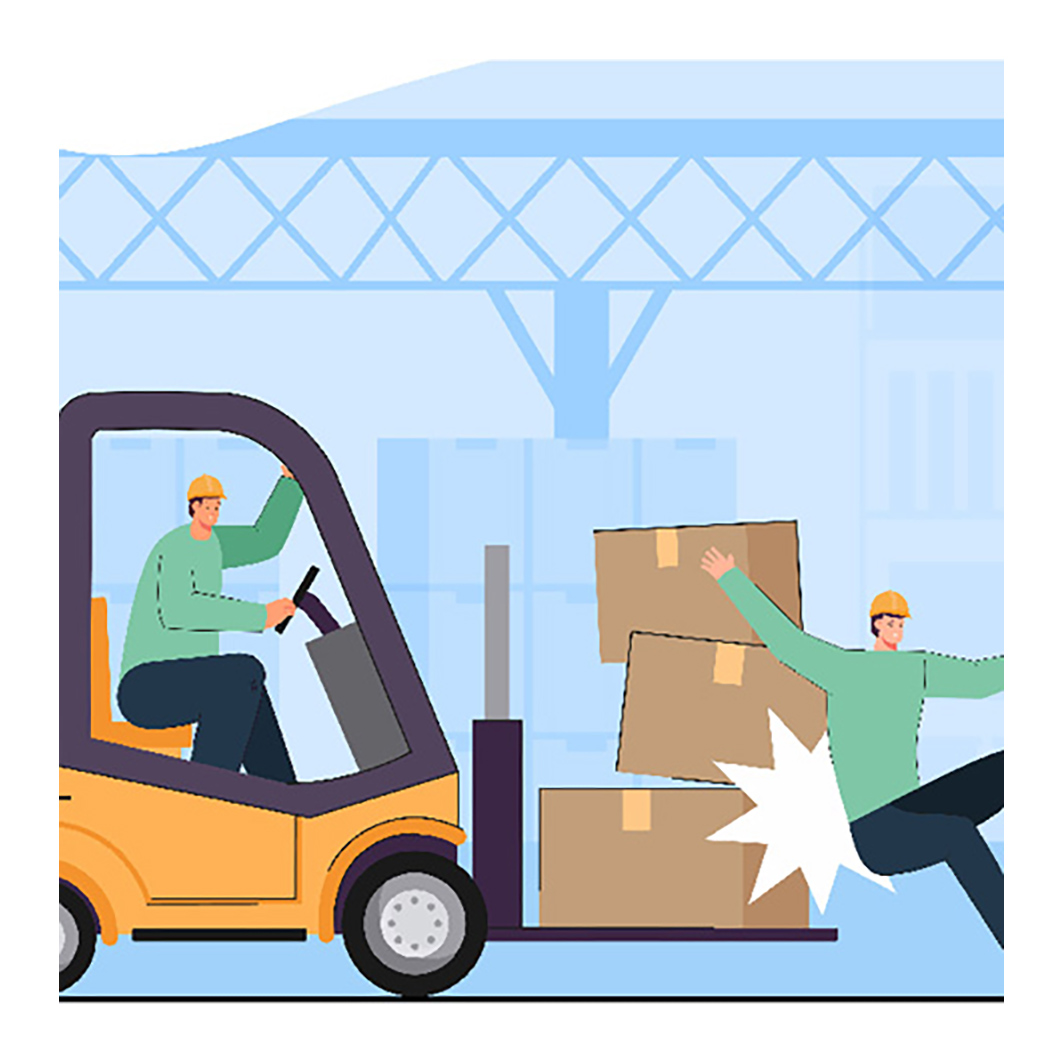
Being struck by a moving vehicle was the second highest cause of fatality in industry in 2019/20. Forklift trucks are a common sight in warehouses. Legally, only people with a forklift training certification are allowed to operate them and no one under the age of 18 is allowed to drive one. Forklift truck accidents can be severe and are usually as a result of lack of training, supervision, vehicle maintenance or poorly marked walkways. The design and layout of the warehouse therefore needs to be carefully planned with vehicle safety a consideration. Throughout the site, there should be prominent speed limit signs that all drivers need to obey and when driving a forklift, they should not exceed 5mph. There should be designated walkways for pedestrians with clearly marked boundaries. As well as displaying safety notices and signs for drivers to be aware of pedestrians, people working on the warehouse floor need to maintain a heightened awareness of forklift operations around them.
Forklifts must also be inspected before every shift. Forklift safety tags that can be displayed on the forklift are a useful tool for confirming these essential safety checks have taken place.
Racking should also be inspected on a regular basis as damage to racking is the leading cause of rack system failure. Racking tags can make this process mush easier – Centurion’ Europe’s racking tags are designed to be fixed to the crossbeams of the racking. The checklist on the insert describes the checks which must be made and inspection details can be recorded. If the racking is deemed to be unsafe, the insert can be removed and replaced with a Do Not Use Unsafe Racking message.
The frequency of inspections varies between warehouses and should be determined by a nominated ‘person responsible for racking safety’ to suit the operating conditions of the warehouse.
Signage
Safety signs, posters and notices have already been frequently referenced; however, it’s worth reiterating just how valuable they can be as a control measure. The Health and Safety (Signs & Signals) Regulations 1996 require employers to ensure that safety signs are provided (or are in place) and maintained in circumstances where there is a significant risk to health and safety that has not been removed or controlled by other methods. This is only appropriate where use of a sign can further reduce the risk. Among the many signs you can expect to see in a warehouse include, racking tags, housekeeping posters, slip danger signs, fire safety signs, temperature controlled storage signs, warning signs for dangerous substances, forklift truck and other machinery safety signs, floor markings, high vis clothing as well as other PPE signs.
Forklifts must also be inspected before every shift. Forklift safety tags that can be displayed on the forklift are a useful tool for confirming these essential safety checks have taken place.
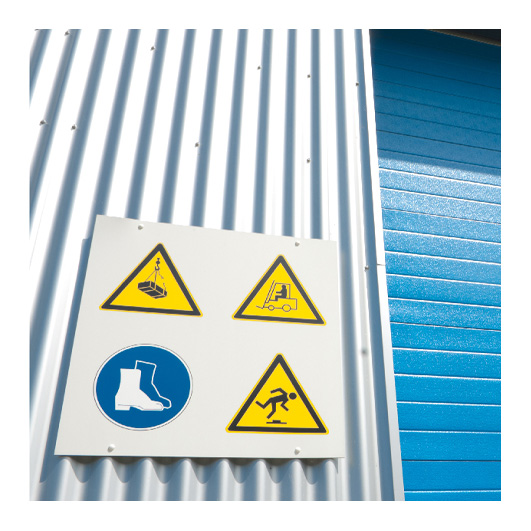
The frequency of inspections varies between warehouses and should be determined by a nominated ‘person responsible for racking safety’ to suit the operating conditions of the warehouse.
Conclusion
When it comes to warehouse safety, there are many common-sense rules to follow that can help prevent the risk of accidents. Good housekeeping includes keeping work areas tidy and free of obstruction. Good organisation means items are stored in assigned places and general fire safety includes ensuring all fire exits are cleared and fire extinguishers and sprinkler systems are not blocked. Always following manufacturer guidelines for any equipment in use and ensure it is maintained with regular safety checks. Keeping risk assessments and employee training refreshed and up to date will also contribute towards a positive safety culture in the warehouse. For further information, the HSE has published Warehousing and storage; a guide to health and safety
Forklifts must also be inspected before every shift. Forklift safety tags that can be displayed on the forklift are a useful tool for confirming these essential safety checks have taken place.
Racking should also be inspected on a regular basis as damage to racking is the leading cause of rack system failure. Racking tags can make this process mush easier – Centurion’ Europe’s racking tags are designed to be fixed to the crossbeams of the racking. The checklist on the insert describes the checks which must be made and inspection details can be recorded. If the racking is deemed to be unsafe, the insert can be removed and replaced with a Do Not Use Unsafe Racking message.
The frequency of inspections varies between warehouses and should be determined by a nominated ‘person responsible for racking safety’ to suit the operating conditions of the warehouse.