The Top 5 Biggest Failings in Lockout, Tagout, Tryout (LOTOTO) And How to Avoid Them
Posted on: 27/02/2025
The Top 5 Biggest Failings in Lockout, Tagout, Tryout (LOTO) And How to Avoid Them
Lockout, Tagout, Tryout (LOTOTO) routines are critical to workplace safety. They are designed to prevent the unexpected release of hazardous energy during equipment servicing or maintenance and are often the line between a routine task and a life-altering accident.
Despite their importance, we see many examples of businesses falling short in implementing robust LOTOTO standards. These failings not only jeopardise employee safety but can also lead to devastating injuries, significant fines and damage to a company’s reputation.
Why It Matters: One of the most fundamental requirements of a successful LOTOTO program is having clear, detailed and written energy control procedures for every piece of equipment. Without these, workers are left guessing how to isolate energy sources, which increases the risk of errors.
This is one area we are challenged on the most when discussing Lockout Tagout. Companies often cite: "it isn't a legal requirement" or "it is too expensive." However, our response is always:
Consider this scenario: A new engineer joins your business. As part of their induction, they receive full training on your company-wide operating procedures. While this ensures they understand the equipment, who can use it, and the importance of lockout procedures, it does not guarantee they are aware of the specific energy control measures required for each machine. In their second week, they are asked to complete a lockout tagout task. However, when they approach the machine to isolate it safely, there is no machine-specific energy control procedure to guide them. Without clear instructions on which isolation points or energy sources must be secured, they cannot ensure the machine is properly made safe. How can the Engineer safely de-energise this machine to safely complete their work?”
Why This Happens:
Top Tip: Health and Safety Managers should conduct a comprehensive audit of all machinery and create or update written energy control procedures. Ensure these documents are specific, clear, and accessible to all employees.
An effective, machine-specific Lockout Tagout energy control procedure will contain:
Why This Happens:
Top Tip: Implement a robust and ongoing LOTOTO training program. Include initial onboarding, regular refresher courses and hands-on demonstrations. Ensure contractors are also trained, as they are often overlooked. One great way to maintain continuous engagement and focus on the importance of effective lockout tagout controls is through your daily meetings or toolbox talks.
Why This Happens:
Top Tip: Reinforce the importance of the ‘Tryout’ phase in training and procedures. Include it as a mandatory checklist and regularly audit compliance.
Why This Happens:
Top Tip: Invest in high-quality LOTOTO equipment tailored to the needs of your business. Conduct regular inspections to ensure equipment remains in good condition and is readily available.
Why This Happens:
Top Tip: Create a culture of accountability by regularly monitoring LOTOTO compliance and addressing non-compliance promptly. Recognise employees who demonstrate strong adherence to safety practices to reinforce positive behaviour.
What Can Happen When It Goes Wrong?
We wanted to highlight a few examples of where Lockout Tagout failings have led to severe consequences for workers and their businesses:
The key is that most Lockout Tagout failings are preventable with the right approach. Taking proactive steps to prevent workplace injuries related to Lockout Tagout is critical for protecting both employees and your business.
Workplace injuries caused by Lockout Tagout failures are not just statistics, they are real people with families, lives and futures that can be changed in an instant. The difference between a normal shift and a life-altering accident often comes down to proactive safety measures.
It’s not enough to have some processes in place – there must be robust and detailed controls culturally embedded throughout the workplace, and workers need to understand why they matter. Skipping steps, rushing jobs, or assuming a machine is safe without testing can have devastating consequences. A strong safety culture means making Lockout Tagout second nature. This includes regular training, clear procedures and the confidence to speak up when something isn’t right. Safety isn’t a box to tick – it’s a commitment to making sure everyone goes home at the end of the day.
Please get in touch with us if you require any support driving Lockout Tagout improvements across your workplace.
Spectrum Industrial: Your Partner in Safety
At Spectrum Industrial, we understand that effective LOTOTO programs require more than just knowledge. They need the right tools and support. Based in Doncaster, UK, we provide a comprehensive range of lockout, tagout, and safety signage solutions tailored to your needs. Whether you’re starting from scratch or looking to improve your existing procedures, our team of experts is here to help.
By implementing robust Lockout, Tagout, Tryout procedures, you’re not just complying with regulations, you’re protecting lives and creating a culture of health and safety.
If you need support with lockout, Tagout, Tryout to improve health and safety in your workplace, contact Spectrum Industrial today.
Lockout, Tagout, Tryout (LOTOTO) routines are critical to workplace safety. They are designed to prevent the unexpected release of hazardous energy during equipment servicing or maintenance and are often the line between a routine task and a life-altering accident.
Despite their importance, we see many examples of businesses falling short in implementing robust LOTOTO standards. These failings not only jeopardise employee safety but can also lead to devastating injuries, significant fines and damage to a company’s reputation.
Failing #1: Lack of Written Energy Control Procedures
Why It Matters: One of the most fundamental requirements of a successful LOTOTO program is having clear, detailed and written energy control procedures for every piece of equipment. Without these, workers are left guessing how to isolate energy sources, which increases the risk of errors.
This is one area we are challenged on the most when discussing Lockout Tagout. Companies often cite: "it isn't a legal requirement" or "it is too expensive." However, our response is always:
Consider this scenario: A new engineer joins your business. As part of their induction, they receive full training on your company-wide operating procedures. While this ensures they understand the equipment, who can use it, and the importance of lockout procedures, it does not guarantee they are aware of the specific energy control measures required for each machine. In their second week, they are asked to complete a lockout tagout task. However, when they approach the machine to isolate it safely, there is no machine-specific energy control procedure to guide them. Without clear instructions on which isolation points or energy sources must be secured, they cannot ensure the machine is properly made safe. How can the Engineer safely de-energise this machine to safely complete their work?”
Why This Happens:
- Lack of awareness about the vital role detailed procedures play in maintaining a safe working environment
- Over-reliance on experienced workers’ knowledge instead of documented procedures
Top Tip: Health and Safety Managers should conduct a comprehensive audit of all machinery and create or update written energy control procedures. Ensure these documents are specific, clear, and accessible to all employees.
An effective, machine-specific Lockout Tagout energy control procedure will contain:
- A unique machine ID or name, along with an image for easy identification
- Information for each energy source or isolation point, including:
- An image of each isolation point
- The energy source involved
- The specific location of the isolation point
- The action required to de-energise the machine (e.g. switch electrical rotary disconnect to off)
- Lockout equipment required to isolate
- How to ‘Tryout’ the machine once safely isolated
Failing #2: Inadequate Training for Workers
Why It Matters: Even the best procedures are useless if workers don’t understand how to apply them. Inadequate training often leaves employees unaware of the risks associated with uncontrolled energy or unsure of the correct LOTOTO steps.Why This Happens:
- High staff turnover leading to training gaps
- Lack of time allocated for training
- Lack of awareness of specific skills required to successfully execute tasks within the company
Top Tip: Implement a robust and ongoing LOTOTO training program. Include initial onboarding, regular refresher courses and hands-on demonstrations. Ensure contractors are also trained, as they are often overlooked. One great way to maintain continuous engagement and focus on the importance of effective lockout tagout controls is through your daily meetings or toolbox talks.
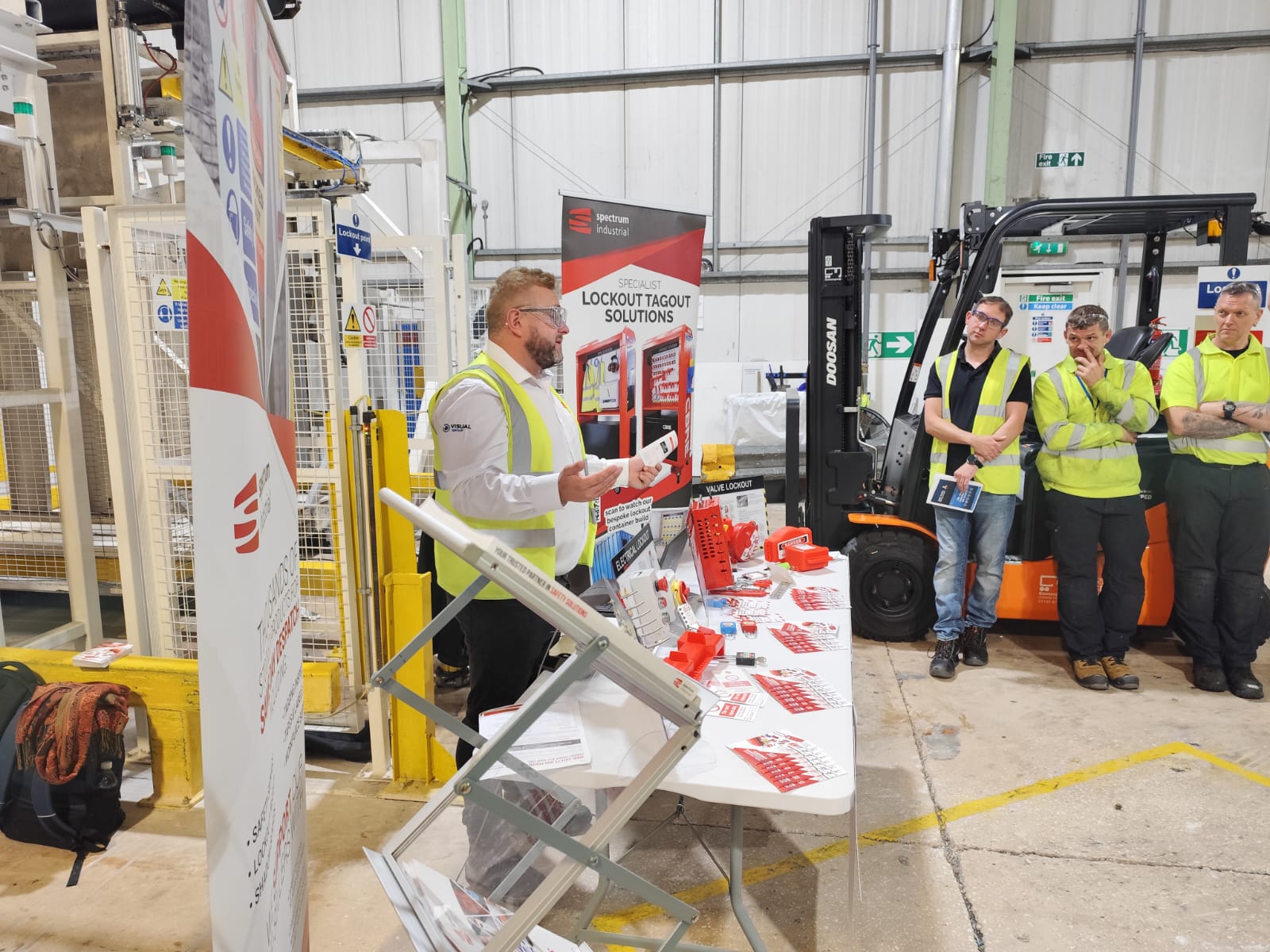
Failing #3: Overlooking the ‘Tryout’ Step
Why It Matters: The ‘Tryout’ step means testing the equipment to confirm it is fully de-energised. This is a crucial yet frequently skipped part of the LOTOTO process. Without it, workers risk interacting with machinery that is still hazardous.Why This Happens:
- Time pressure leading to skipped steps
- Misconceptions that locking out equipment alone is sufficient
Top Tip: Reinforce the importance of the ‘Tryout’ phase in training and procedures. Include it as a mandatory checklist and regularly audit compliance.
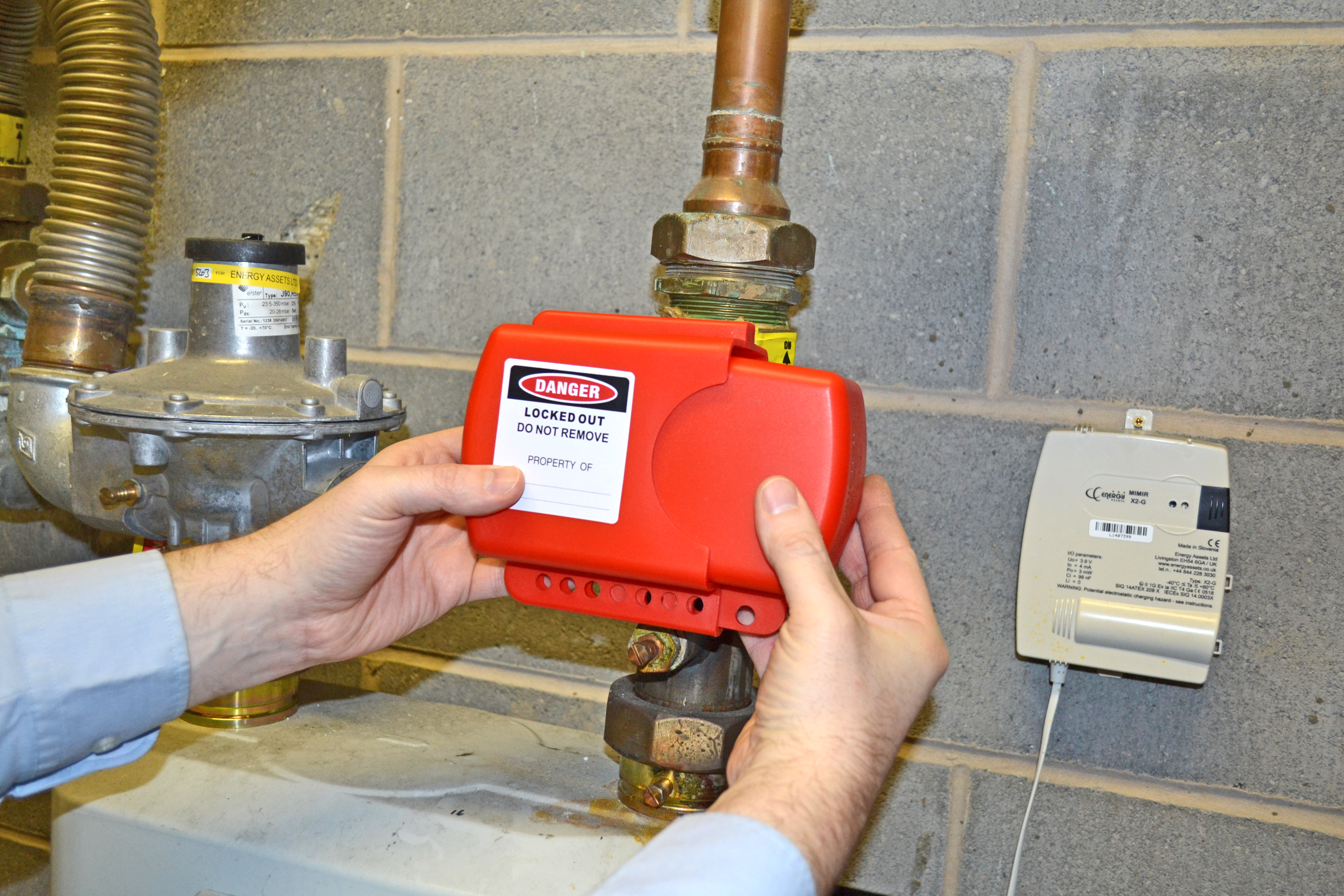
Failing #4: Using Improper or Insufficient Equipment
Why it matters: Using makeshift or inappropriate lockout devices can undermine the entire LOTOTO process. Equipment such as fragile tags, ill-fitting locks, or missing devices leave energy sources inadequately controlled.Why This Happens:
- Lack of investment in proper LOTOTO equipment.
- Poor inventory management leading to missing or inadequate tools.
Top Tip: Invest in high-quality LOTOTO equipment tailored to the needs of your business. Conduct regular inspections to ensure equipment remains in good condition and is readily available.
Failing #5: Inconsistent Enforcement of Procedures
Why It Matters: Even with solid procedures and training, inconsistent enforcement can erode a safety culture. Workers may skip steps or bypass procedures if they see others doing the same without consequence.Why This Happens:
- Managers prioritising productivity over safety.
- Lack of accountability or disciplinary measures for non-compliance.
Top Tip: Create a culture of accountability by regularly monitoring LOTOTO compliance and addressing non-compliance promptly. Recognise employees who demonstrate strong adherence to safety practices to reinforce positive behaviour.
What Can Happen When It Goes Wrong?
We wanted to highlight a few examples of where Lockout Tagout failings have led to severe consequences for workers and their businesses:
- In one HSE case, a manufacturing company was fined more than £360,000 after one of its employees lost a finger in machinery. After the hearing, HSE inspector Rebecca Gibson said, “This unnecessary incident highlights the duty on employers to ensure that there are robust procedures in place relating to maintenance activities. If an appropriate ‘lock out tag out’ procedure had been produced and implemented and with suitable training, the serious injury would have been avoided.”
- Following a catastrophic incident in an American bottling plant in 2012, the company was fined for not training temporary employees on utilising Lockout Tagout routines. This video is a harrowing watch, but clearly highlights the importance of Lockout Tagout.
Summary
The key is that most Lockout Tagout failings are preventable with the right approach. Taking proactive steps to prevent workplace injuries related to Lockout Tagout is critical for protecting both employees and your business.Workplace injuries caused by Lockout Tagout failures are not just statistics, they are real people with families, lives and futures that can be changed in an instant. The difference between a normal shift and a life-altering accident often comes down to proactive safety measures.
It’s not enough to have some processes in place – there must be robust and detailed controls culturally embedded throughout the workplace, and workers need to understand why they matter. Skipping steps, rushing jobs, or assuming a machine is safe without testing can have devastating consequences. A strong safety culture means making Lockout Tagout second nature. This includes regular training, clear procedures and the confidence to speak up when something isn’t right. Safety isn’t a box to tick – it’s a commitment to making sure everyone goes home at the end of the day.
Please get in touch with us if you require any support driving Lockout Tagout improvements across your workplace.
Spectrum Industrial: Your Partner in Safety
At Spectrum Industrial, we understand that effective LOTOTO programs require more than just knowledge. They need the right tools and support. Based in Doncaster, UK, we provide a comprehensive range of lockout, tagout, and safety signage solutions tailored to your needs. Whether you’re starting from scratch or looking to improve your existing procedures, our team of experts is here to help.
- Lockout Tagout Site Surveys: Our surveys will review your LOTOTO process for when machinery is undergoing repair or maintenance and advise on the process and products required to ensure machinery is safely isolated during repair or routine maintenance
- Lockout Tagout Training: Our team offers training programmes for our resellers and their sales teams, as well as mobile training events for staff to get hands-on with our products
By implementing robust Lockout, Tagout, Tryout procedures, you’re not just complying with regulations, you’re protecting lives and creating a culture of health and safety.
If you need support with lockout, Tagout, Tryout to improve health and safety in your workplace, contact Spectrum Industrial today.